Characterization of fuel cell systems: the auxiliary test bench built by H2Pulse
Fuel cells represent one of the most promising technologies for the energy transition in terms of the consumption of clean and renewable energy such as hydrogen. In order to guarantee optimal performance and extend the life of fuel cell systems, it is essential to carefully select the various auxiliaries that make them up. Among these components, the humidifier plays a crucial role in providing the humidity necessary for the proper functioning of the cell core membrane. It is in this context that the test bench for fuel cell auxiliaries, designed by H2Pulse, is an essential tool for the characterization of these systems.
1. Presentation of the humidification test bench
The main aim of the test bench developed by H2Pulse is to test and optimize the humidification aids used in fuel cell systems. This project followed various test campaigns dedicated to testing passive humidifiers without PFAS. The entire design, development, debugging and testing process was handled by the H2Pulse engineering team, located at the Francazal airbase (Toulouse-Cugnaux), in the south of France.
Designed to provide relevant data and improve the efficiency of fuel cell systems, the test bench is a complex piece of equipment that offers great flexibility in terms of configurations and test conditions. It is composed of two separate lines: a dry line and a wet line, independent, allowing to simulate a wide range of fuel cell operating conditions and to study the impact of this auxiliary on the overall performance of the system.
2. The essential role of the passive humidifier
The passive humidifier is one of the most important auxiliaries in fuel cell systems. Its main function is to humidify the dehydrated air entering the fuel cell, so as to reinject it into the cell without compromising the integrity of the electrolytic membrane. Indeed, humidity plays a crucial role in the correct operation of the cell, and in particular in the proton conductivity of the solid electrolyte; and a lack of humidity can lead to a drop in performance, or even to irreversible damage to the cell.
The test bench designed by H2Pulse enables the passive humidifier to be tested under conditions similar to those encountered when using it in real systems. By simulating different pressures, flow rates, temperatures and humidity levels, the bench enables us to characterize the operation of this key auxiliary and to better understand the interactions between the air entering and leaving the cathode.
3. Humidification test bench operation
The test bench has two separate lines: a dry line and a wet line. The dry line simulates the cathode inlet at the compressor outlet (relative humidity at 0%). It is emulated by a heater and a pressure regulation valve. The wet line corresponds to the reinjection of the water produced by the operation of the cell at the cathode exhaust.
Flow and pressure capacity:
The two test bench lines can achieve a dry air flow rate of 500 NL/min. In terms of pressure, the lines are designed to withstand a maximum pressure of 2.5 bara. These conditions make it possible to emulate stacks of up to 10 kW, under conditions equivalent to those found in industrial applications.
4. Humidity management and test conditions
The main function of this test bench is to precisely control the humidity of the wet line (cathode exhaust), a crucial variable for the correct operation of fuel cells. Indeed, fuel cells require a specific environment to operate efficiently, particularly with regard to the humidity of the air that comes into contact with the electrolytic membrane.
The test bench allows a relative humidity of 100% to be achieved at a temperature of 90°C, a pressure of 1.5 bara and a flow rate of 240 NL/min, thanks to two active humidifiers.
In addition, higher flow rates can be achieved while maintaining 100% relative humidity by adjusting temperature and pressure: by increasing pressure or decreasing temperature, the test bench requires less water injection to maintain a high level of relative humidity.
5. Importance of synergies between auxiliaries
One of the keys to optimizing fuel cell systems lies in improving synergies between the various auxiliaries. H2Pulse emphasizes that fuel cell performances depend not only on the heart of the system, i.e. the fuel cell itself, but also on how the auxiliaries interact to maintain optimal operating conditions. This includes elements such as humidifiers, thermal management systems, compressors and hydrogen storage tanks.
Optimizing these synergies is essential for improving the durability and efficiency of fuel cell systems, particularly in mobile applications (vehicles, drones, etc.) or stationary applications (power generation plants). The test bench developed by H2Pulse enables us to gain an ever better understanding of how these auxiliaries interact, and to find solutions for improving their collective performance.
6. Conclusion: Towards an optimized fuel cell
In conclusion, the test bench developed by H2Pulse represents an essential tool for characterizing and optimizing fuel cell systems. Thanks to its ability to simulate a wide range of pressure, temperature and humidity conditions, the bench enables in-depth study of the humidification auxiliary, the optimization of which is crucial to improving overall fuel cell efficiency.
H2Pulse is convinced that the future of fuel cell systems lies in the continuous improvement of synergies between the various components, in order to maximize the performance and durability of these technologies. The test bench plays a central role in this process, providing invaluable data that will enable us to design ever more efficient systems tailored to specific user needs.
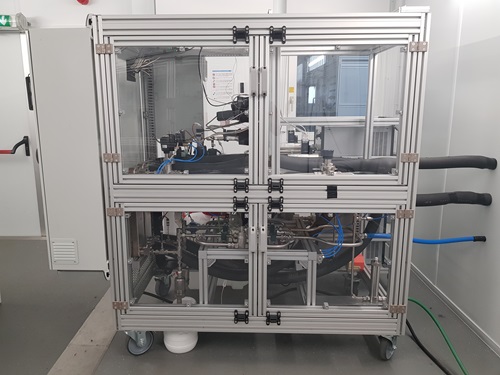